Unearthing the ‘why’ behind root cause analysis
In this blog, NQA Regional Assessor Marc Pathy introduces root cause analysis in the context of ISO management systems. Discover why businesses should find the root cause, what exactly non-conformities are, and a real-life scenario to help.
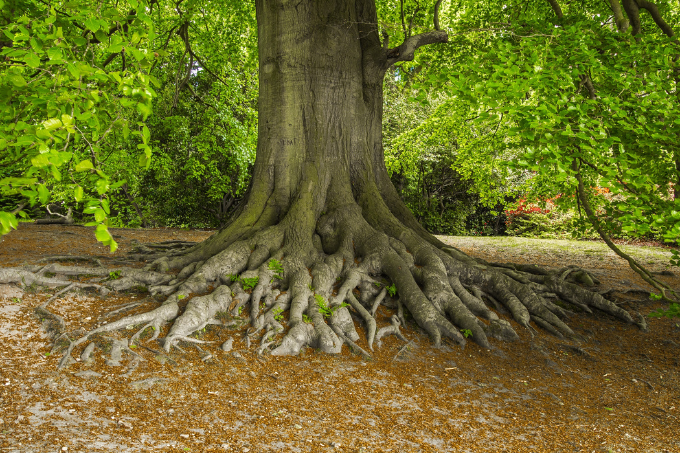
Root cause analysis in ISO management systems
Whether your business already has ISO standards or is a total novice, root cause analysis is a term you will come across plenty.
Question #1: Why should we find the cause(s) of a non-conformity?
First of all, let’s define ‘non-conformity’.
Non-conformity is the failure to meet a management system requirement. There are two classifications of non-conformities:
-
Major – if one or more parts of the management system are missing or there is a complete breakdown.
-
Minor – an incident that doesn’t result in the management system totally failing or breaking down.
It’s worth noting that non-conformance varies between standards.
Non-conformance in ISO 9001 (Quality Management) might look like a manufacturing procedure leading to a reduction in quality – an issue that the organisation doesn’t deal with immediately.
On the other hand, ISO 14001 (Environment Management) non-conformity could be a business keeping machinery maintenance records. However, a few check-ups haven’t been noted down.
In ISO 45001 (Health & Safety Management), non-conformity may involve protective equipment not functioning properly, or an organisation failing to apply regulatory requirements.
So, back to the question: Why should we find the cause(s) of a non-conformity?
The answer is actually very simple. All 3 ISO standards we talked about above – spanning quality, environmental, and health and safety – require root cause analysis.
A vital part of ISO 9001, ISO 14001 and ISO 45001 is finding the root cause of the non-conformity.
Question #2: Why is root cause analysis required in these 3 ISO standards?
Root cause analysis is recognised internationally as best practice when faced with a problem.
(As we went through in Question 1, the ‘problem’ – or non-conformity – can be major or minor.)
Becoming ISO-certified is one of the leading ways to prove your organisation follows best practices. An ISO standard gives the ‘seal of approval’ that your management system works as it should – for the benefit of the business, customers and beyond.
ISO standards are all about following best practices, with root cause analysis being one of them.
Question #3: Why can’t you find a solution without identifying the cause?
It’s critical to discover the root cause of non-conformity.
If you don’t identify the cause of a non-conformity, you will only solve what you think or assume is the problem. As a result, you could end up addressing a consequence rather than the actual cause.
By not dealing with the underlying cause, the same problem might end up recurring indefinitely.
Think of root cause analysis as correcting not only the symptom but the problem as well.
An example of not investigating the root cause
Below is a day-to-day scenario that compares fixing the issue without identifying the cause vs. carrying out a root cause analysis.
Scenario 1: Fixing the issue without identifying the root cause
-
Part 1: The red brake warning light starts flashing on your dashboard. No matter what you do, it won’t switch off.
-
Part 2: You take a look at the brake pads and disks. They appear to be fairly worn, and so you decide to change them.
-
Part 3: You invest hours of time and effort sourcing the parts, removing the disks and pads, and replacing them.
-
Part 4: You test drive the car. The red brake warning light comes on immediately and won’t switch off – no matter what!
Scenario 2: Carrying out a root cause analysis
-
Part 1: The red brake warning light starts flashing on your dashboard. No matter what you do, it won’t switch off.
-
Part 2: You check the brake light bulb and find it has blown. You go online and source a new brake light bulb.
-
Part 3: You replace the current brake light bulb and go on a test drive. Good news: the warning light has switched off!
The moral of the story: save yourself trouble and expense by always delving into the root cause.
Final thoughts from NQA
When dealing with a problem – whether it be a major or minor non-conformity – it’s always worthwhile unearthing the root cause.
Alongside saving resources in the long term, your business can bolster its chances of ISO certification!
Stay tuned for another blog post from Marc Pathy, walking us through the various methods for effective problem-solving.
Thinking of gaining UKAS-accredited ISO certification? Get in touch with our sales team today.
Get up-to-speed with the ISO standard you have in mind. Discover our global virtual ISO training.