How to Implement ISO 9001 Into Your Business: A Step-by-Step Guide
Whether you’re a small business or a large corporation, ISO 9001 can help you streamline processes, improve product quality, and drive continuous improvement.
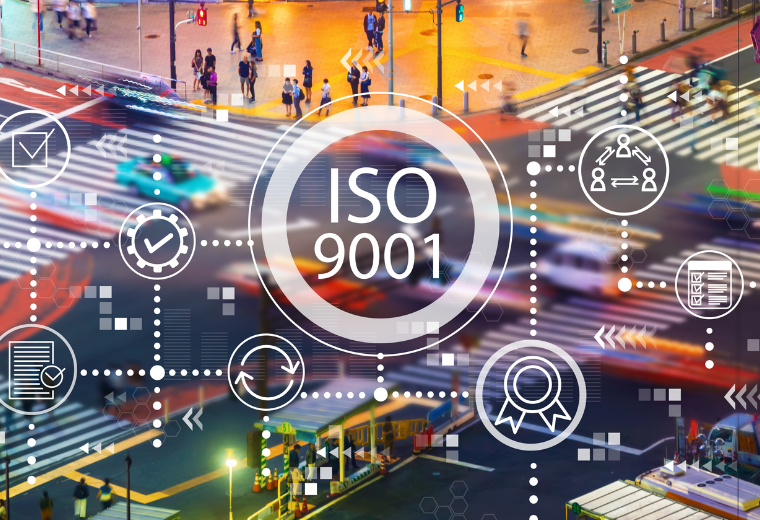
In today’s competitive business environment, quality management is key to building trust, ensuring customer satisfaction, and maintaining operational efficiency. One of the best ways to achieve this is by implementing ISO 9001:2015, the internationally recognised standard for Quality Management Systems (QMS).
Here’s a step-by-step guide on how to implement ISO 9001 into your business.
1. Understand ISO 9001 and its benefits
Before diving into implementation, it’s essential that you have a clear understanding of what ISO 9001 is and how it can benefit your business. What are you hoping that it will achieve? ISO 9001 sets out criteria for a QMS and is based on a number of quality management principles, including a strong customer focus, leadership involvement, a process-based approach, and continuous improvement.
Benefits include:
-
Enhanced product/service quality
-
Increased customer satisfaction
-
Streamlined operations and reduced waste
-
Improved compliance with regulations
- Greater business credibility
2. Leadership commitment
In order to successfully implement and maintain ISO 9001 within your organisation you’ll need total commitment from top management. Not only is it a requirement of the standard but leadership needs to be involved from the start as their support ensures that the necessary resources, time, and authority for changes to take place can be given.Management should:
-
Understand the requirements of ISO 9001
-
Communicate the importance of quality management to the entire team
-
Set quality objectives that align with the business’s strategic goals
-
Allocate resources for training, implementation and ongoing maintenance
3. Conduct a gap analysis
Completing a gap analysis will help you identify areas where your current processes may fall short of ISO 9001 requirements. You’ll need to review your existing processes, policies, and procedures to determine what needs improvement. This will then serve as the foundation for your implementation plan.
Key areas to assess:
- Process control
-
Customer satisfaction and feedback
-
Risk management
-
Documentation practices
-
Internal audits and corrective actions
- The results of the gap analysis will help you to prioritise the areas that require the most attention.

4. Create an implementation plan
With the gap analysis finalised, you can move forward to create a detailed implementation plan. This plan should define the specific steps you need to take to achieve ISO 9001 certification, including any:
-
Process updates: Identify which processes need improvement or documentation.
-
Timeline: Establish a realistic timeline for each phase of implementation.
-
Responsibilities: Assign roles to team members who will lead different parts of the implementation.
- Training needs: Ensure that employees at all levels understand ISO 9001 and their role in maintaining quality throughout
5. Document your QMS
One of the core requirements of ISO 9001 is having a well-documented Quality Management System. Documentation ensures consistency, accountability, and a basis for continuous improvement.
Some key documents that you may want to consider could include:
-
A quality manual
-
Your quality policy and objectives
-
Process flowcharts and descriptions
-
Standard operating procedures (SOPs)
-
Records of any internal audits, findings and corrective actions taken
It’s important to ensure that your documentation is clear, accessible, and regularly updated. This will not only help during the certification process but also with long-term compliance.

6. Train your employees
Training is a critical step in ensuring that ISO 9001 becomes a permanent part of your company culture. Employees need to understand both the importance of quality management and their specific roles within the QMS.
You may want to think about training staff on:
-
The basics of ISO 9001 and its purpose
-
How to follow documented processes and procedures
-
Reporting non-conformities and corrective actions
- The importance of customer satisfaction and feedback
7. Implement and monitor your QMS
Once processes are documented and your team is trained, it’s time to implement your QMS. Start by applying the new or revised procedures across the organisation, ensuring that everyone is following them consistently.To know that it’s working for your business it’s important to monitor and measure the performance of your QMS regularly. The standard is designed to be flexible so that it can be moulded to your specific company and doesn’t need to be ridged or restricting.
What could you look at monitoring?
-
Internal audits: Regular internal audits will help you to check if the system is being followed and identify areas for improvement.
-
KPIs: Use Key Performance Indicators (KPIs) to measure performance against your quality objectives.
-
Customer feedback: Actively gather feedback from customers and make adjustments to your processes based on their needs.
8. Conduct internal audits and review
Internal audits are a requirement of ISO 9001 and help ensure that your QMS is functioning effectively. These audits should be conducted by competent employees who can objectively assess the system’s performance.After internal audits, organise management reviews to evaluate the findings and make strategic decisions and actions.
Management reviews should focus on:
-
Audit results
-
Customer feedback and complaints
-
Process performance and product conformity
-
Opportunities for improvement
- Risk mitigation
9. Take corrective actions
When issues are identified, whether through internal audits or customer feedback, it’s important to take corrective action. This involves identifying the root cause of the problem and implementing measures to prevent it from recurring in the future.
Documenting these actions is essential, as it demonstrates your commitment to continuous improvement – a core principle of ISO 9001.
10. Get certified
Once your QMS has been implemented and tested through your own internal audits, you can apply for ISO 9001 certification with an accredited certification body (NQA is accredited by UKAS). The certification body will conduct an external audit to assess whether your QMS meets the requirements of the ISO 9001 standard.
Your external audit typically takes place across two stages:
Stage 1: A preliminary review of your documentation and QMS.
Stage 2: A full audit to ensure your system is functioning as intended.
After successfully passing the audit, your business will receive ISO 9001 certification, which is valid for three years, with annual surveillance audits to ensure continued compliance.
11. Maintain and improve your QMS
ISO 9001 is not a one-time certification or ‘tick-box’ experience but an ongoing commitment to quality management. You’ll need to maintain and continually improve your QMS by:
-
Conducting regular internal audits and management reviews
-
Responding to changes in business processes or customer needs
- Encouraging a culture of continuous improvement within your team
Conclusion
Implementing ISO 9001 into your business is an investment in quality, efficiency, and customer satisfaction. You can build a robust QMS that meets international standards and supports long-term success.
Not only will ISO 9001 certification boost your company’s credibility, but it will also help you streamline and refine your operations, reduce waste, and exceed customer expectations.
Whether you're a young or a well-established company, ISO 9001 can transform the way you approach quality, making it a vital tool for growth and sustainability.

Author:
Clark Boles, APP Member – CBO Associates Ltd.

Ready to make the first step towards certification and success? Get in touch with our team.

Fill out our quick form and get a quote for ISO 9001 certification today.