Effective Corrective Action Plan
19 October 2016
As an Assessor and previously as a Systems Manager, Joe Kelly firmly believes in and understands the effectiveness of a robust corrective action plan when something has gone wrong; whether it be quality, environmental or health and safety.
What Is A Corrective Action Plan?
Sometimes, when things go wrong in an organization, they’re minor and easily corrected. However, in other circumstances, some situations, events and actions can occur that prove to be more systematic in nature. If they’re not handled properly, they can leave the entire organization susceptible to the negative consequences they bring with them.Naturally, for any organization that wants to maintain its competitive edge and encourage customer loyalty, a quality management system is a proven way to check that its products and/or services are of a sufficiently high quality and meet all regulatory and compliance standards. However, when problematic concerns or instances of non-compliance arise, a corrective action program is by far one of the most effective measures used to address a given problem.
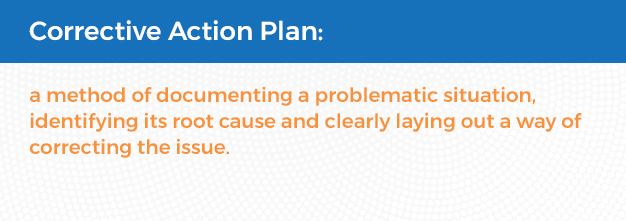
Strictly speaking, a corrective action plan is a method of documenting a problematic situation, identifying its root cause and clearly laying out a way of correcting the issue. In addition, to check on the effectiveness of the proposed corrective action, it should contain some method that allows the organization to verify that the new action works appropriately.
When Do You Need A Corrective Action Plan?
There’s a great deal of debate over when a corrective action plan is needed. To help clarify this issue, keep in mind that the inherent nature of a corrective action plan is to find and correct problems that are of a systematic nature. These types of problems aren’t likely to correct themselves. At its core, a corrective action plan is most needed when problems arise that pose a real threat to an organization’s quality management system or health and safety management.Some examples of when a corrective action plan could be of assistance include incidents when nonconformity or poor quality is discovered as the result of an audit or customer complaint. Of course, adverse conditions can trigger a corrective action plan at any point, but an effort should be made to discern whether the problem is a one-off aberration or a systematic failure.
Remember that with many corrective actions plans, insufficient data about problems and/or a failure to check on the effectiveness of corrective actions can detract from their usefulness as well as from the likelihood that they’ll result in system-wide improvements. However, once an organization has determined an issue is systematic, it is essential that the problem is immediately stopped from accelerating and where applicable satisfying customers. It is also important to establish the correct root cause, implement effective corrective action and then verifying the effectiveness of that corrective action.
How To Create A Corrective Action Plan
Joe believes a five-step approach of effective corrective action is the best way forward. Here are some headings that should appear in any corrective action / accident form that you keep a record.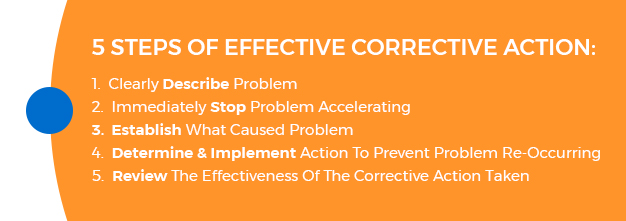
Step 1: Clearly Describe Problem
Example (a): Employee falls down a hole on a workshop floor, excavated by contractors — making this a problem concerned with the management of environmental health and safety.Example (b): Wrong item sent to customer — making this a problem related to quality management.
Step 2: Immediately Stop Problem Accelerating (Commonly Referred To As “Containment Action”)
Example (a): Barrier the hole to prevent further employees for falling down the hole.Example (b): Order correct item. Have wrong item collected. Send correct item ASAP.
Step 3: Establish What Caused Problem (Commonly Referred To As ‘Root Cause’)
There are a number of tried and tested techniques available to use to help establish root cause; of which training should be given to the people in an organization who would have this responsibility e.g. 5 Why’s. It is often far too easy to just state ‘human error.’So What Are The 5 Why’s?
5 Whys is an iterative interrogative technique used to explore the cause-and-effect relationships underlying a particular problem. The primary goal of the technique is to determine the root cause of a defect or problem by repeating the question "Why?" Each question forms the basis of the next question.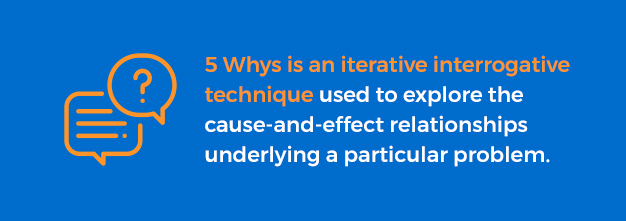
The "5" in the name derives from an anecdotal observation on the average number of iterations needed to resolve the problem.
Here Is An Example Of A CNC Machine That Stopped Mid Operation:
"Why did the machine stop?" The circuit has overloaded, causing a fuse to blow."Why is the circuit overloaded?" There wasn’t enough lubrication on the bearings, so they locked up.
"Why was there not enough lubrication on the bearings?" The oil pump on the machine was not circulating sufficient oil.
"Why is the pump not circulating sufficient oil?" The pump intake was clogged with metal shavings.
"Why is the intake clogged with metal shavings?" Because there was no filter on the pump. This is the root cause.
Example (a):
Why did the employee fall down the hole? The hole had no barrier & no communication to staff that such works were taking place.
Why were there no barrier & no communication? Contractor assigned to excavate hole entered the premises unannounced & commenced works without making their presence known.
Why did they not report to reception / make their presence known & no communication? No one informed the contractor when to arrive & processes on site.
Why was the contractor not informed? No system in place or Permit to Work for managing contractors on site. This is the root cause.
Example (b):
Why was the wrong item ordered & sent? Wrong details entered into system by new member of staff unfamiliar with company’s products.
Why was it possible to enter the wrong details? System does not prompt to check & confirm details with the customer & allows any member of staff to take orders. This is the root cause.
Step 4: Determine And Implement Action To Prevent Problem Re-Occurring (Commonly Referred To As Corrective Action)
Example (a): Implement Permit to Work System, purchase site signage to instruct all contractors to enter via reception & communicate these arrangements to contractors before they come on site.Example (b): Add check into system that prompts checking with the customer what they ordered. Add log-in to system with competence requirements required to be given a log in.
Step 5: Review The Effectiveness Of The Corrective Action Taken — i.e. Did It Work?
This is essentially a small audit of the above proposed corrective actions; by firstly checking that they were actually carried out and then looking for examples of similar activities that have taken place since and verify that the initial problem did not re-occur. This step can be justifiably left over for several months to allow sufficient time to pass. It’s to check that the corrective actions have been imbedded properly.Example (a): Check that a Permit to Work System has been implemented and suitable site signage purchased and fitted. Then look for work that has been done on site checking that the arrangements had been communicated to the contractors before they come on site, they signed in at reception and were not permitted to carryout enter works until they had been inducted and permit to work issued.
Example (b): Check that new step has been added into system that prompts checking with the customer what they ordered. Check that a log-in to system has been added with competence requirements required for such. Then look at the newest employees to ensure that they have the correct competence for any log in that they may have been given.
Sign Up To InTouch For More Corrective Action Plan Information
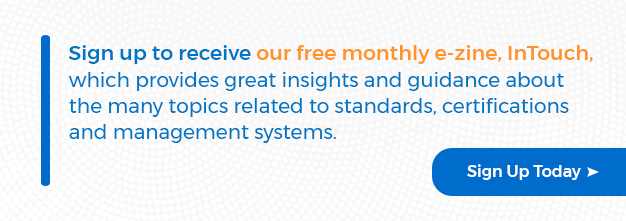
Sign up to receive our free monthly e-zine — InTouch — which provides great insights and guidance about the many topics related to standards, certifications and management systems. Get timely advice from technical experts covering best practices and techniques, as well as alerts on the latest updates and changes to environmental and health and safety legislation.
To learn more about NQA and our services, contact us today.Authored by: Joe Kelly, NQA Assessor